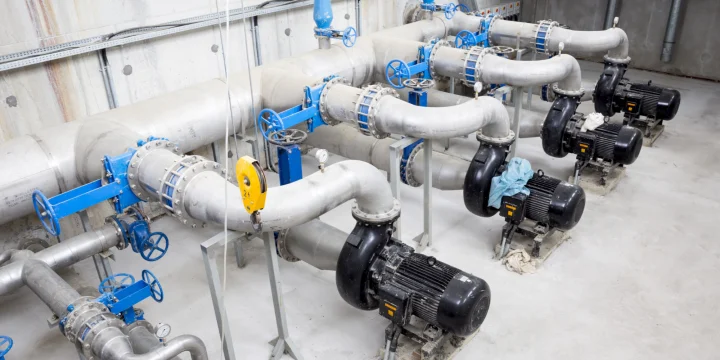
Pump Health Monitoring
Challenge
In process industries such as oil and gas, pharmaceutical and chemical, it is essential to maintain and prolong the lifetime of critical assets including pumps, valves, heat exchangers and compressors. Process companies need better insight into the condition of pumps and other assets. The goal is to gain a clearer understanding of when pumps are not operating efficiently–and the root cause of the degraded performance–instead of waiting until there is a catastrophic failure. Optimizing asset maintenance saves time and money.
Pumps can break down for a number of reasons; ranging from faulty operation, to lack of needed maintenance, to operating outside specifications. Traditionally, process companies have run their pumps to failure, with another pump taking over while removing the broken one from operation to repair. The maintenance cost is high due to the repair being unexpected. It can be cumbersome to make sure they have the spare parts needed to fix the pump on hand. Any delays lead to lost revenue and the potential for environmental and safety threats.
On the other hand, using scheduled maintenance for these assets results in unnecessary work; therefore, planned maintenance is no panacea.
A large U.S. oil and gas company was experiencing unplanned pump downtime of a centrifugal fixed pump. The downtime for this pump was running at about 10 hours per event on average. The company wanted a better way to monitor the health of all of its pumps, enabling it to avoid unplanned downtime while not incurring the inefficiencies of scheduled maintenance.
The company wanted to use leading and lagging performance indicator data to get insight into the pump’s operation. Previously, the company was unable to monitor the health of any of its pumps, only reacting to unplanned failures. The engineers did not have a view into pump health as it was too complex a task for spreadsheets to perform.
Solution
Using Seeq, the solution was to implement condition-based monitoring analysis to understand pump health across hundreds of pump assets. The two major pump performance indicators considered were percent time in a poor mode of operation and percent violation from the threshold.
The Seeq approach can be used by the company’s operators, reliability engineers, process engineers and data science teams. Now, they access the data, which flows into a predictive model in Seeq, enabling them to predict pump failures before they happen.
The Seeq Journal capability enables continuous improvement, empowering teams to go step-by-step through the data, understanding the logic that was applied and making adjustments where necessary to protect pump health.
The Seeq analysis is trusted by both the operating engineering team and the data scientists, who reside on the IT side. Seeq enables both sides to see trends, go back to the source data and schedule repairs when needed. They trust data from Seeq, and are confident they will not schedule a maintenance crew unless the repair is truly needed–a major shift in operation and culture.
Results
The oil and gas company has now reduced the likelihood of pump failure, saving costs due to lost production and manpower per event, per asset. Professionals and engineers from operations and IT are working together and trusting the same data sets, driving better, more holistic decisions. Teams receive a daily health score of their pumps, giving visibility into problems so they can be proactive. The company is planning to expand its use of Seeq to other types of key assets, which it expects will enable proactive maintenance with the potential to save much time and money.
Data Sources
- Asset Management Software: Maximo
- Lab Management Information System
- Process Data Historian: OSIsoft PI
Data Cleansing
- Move times when the pump is not running.
- Remove noise and dropouts with agile filter.
- Splice bad, negative values from flow meter with zero.
Calculations and Conditions
- Histogram displaying time of pump in mode of operation, good and “poor.”
- Percentage of time calculation in different “poor” modes of operation.
- Percentage of time calculation of the magnitude of violation during the “poor” modes of operation.
- Daily health score.
Reporting and Collaboration
- Dashboard with automatic updates to show pump health across all assets using Seeq Organizer Topic.
- Seeq Workbench Analysis to troubleshoot and refine calculations.
- Process, reliability, surveillance and operational excellence engineers use Seeq Workbench for Root Cause Analysis (RCA).