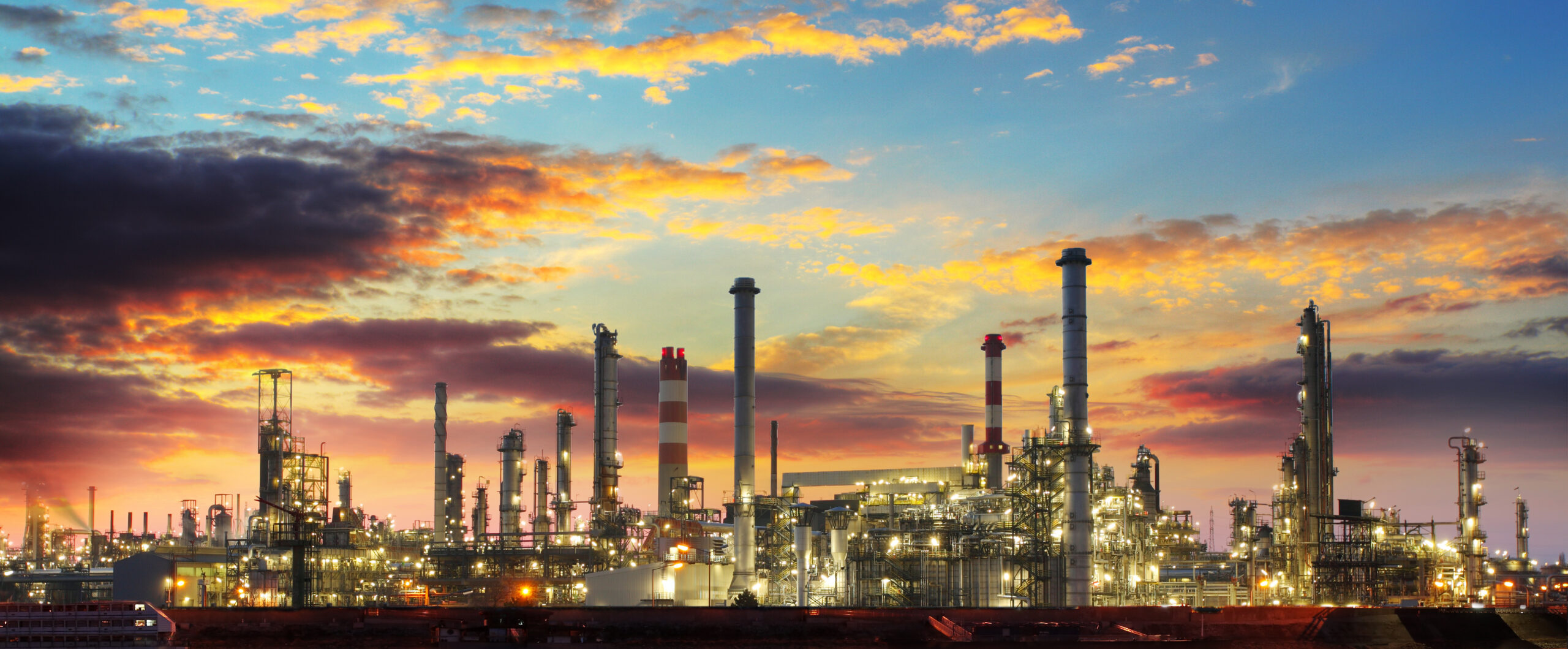
Loss Monitoring and Categorization
Challenge
All manufacturing industries suffer a variety of different performance losses including production losses, product quality losses, energy losses, raw materials losses, environmental/regulatory losses and others. These losses can negatively impact profitability, environmental stewardship, and even license to operate.
To minimize the negative impact, these types of losses should be identified, investigated, categorized, and summarized to be used for performance benchmarking, annual planning and capital project justification. Process engineering teams have traditionally done this via ad-hoc, manual methods that are cumbersome and time-consuming.
Manufacturers of all types need a better way to track and categorize performance losses to identify problem areas and justify improvement projects. Process engineers can spend up to one week per month aggregating loss data for just a single unit.
A manufacturer needed a way to gain insight into the leading causes of production losses, finding those times when equipment was not running at capacity and categorizing the loss by reason. They desired a quick, easy way to summarize the quantity of production losses caused by a given category to inform potential capital investments and ongoing improvement projects.
Solution
The engineering team leveraged Seeq advanced analytics to logically identify and quantify performance-loss events. The process subject matter experts assigned a loss category to each event, using Scorecard Metrics and Histograms to aggregate losses, enabling them to spot trends and zero in on equipment or operations causing substantial productivity loss.
Seeq Workbench tools were used to identify, categorize and summarize performance losses. The summarized analysis was placed in a Seeq Organizer Topic for automatically updating periodic reports with easy collaboration and sharing capabilities.
Losses were identified using Seeq tools to compare actual operation to the ideal and create conditions for when the two modes differ. Losses were categorized using Seeq conditions, where events can be placed in the correct categorical buckets either manually by a console operator or logically based on configured thresholds.
Results
Using Seeq, the engineering team created Performance Loss Summary Reports with color-coded scorecards and charts to draw attention to bad actors and deviations from plans.
Being able to automatically generate these reports as needed (as opposed to compiling them manually each reporting period) can return savings of one to five days of the engineers’ time per unit per month–time they get back to work on improvement projects and other value-added activities. The easily-exportable historical loss data enables engineers to spend more time engineering production optimization projects and less time developing the cost justifications.
Data Sources
- Honeywell PHD, OSIsoft PI, or other Process Data Historian.
- Connection to operator shift logs or shutdown tracking database.
Data Cleansing
- For identifying/categorizing performance losses, time periods when operation was at or better than some target value are ignored since they do not negatively impact profitability.
Calculations and Conditions
- Value Search was used to identify when the manufacturers production rate was less than their target value.
- Composite Conditions were used to intersect loss events with the end/start of reporting periods, to correctly account for losses that spanned multiple months.
- Signal from Condition was used to calculate the quantity of production loss due to each event.
- Custom Conditions were used to categorize the loss events into reason code buckets provided by the SME.
- Formula was used to flag any loss events that had not yet been assigned a reason code.
- Histograms and Scorecard Metrics were used to create graphical and tabular summary visuals of losses from the various categories.
Reporting and Collaboration
- A monthly report was configured in Seeq Organizer Topic. Presentation View was utilized for easy sharing during meetings with the operations business team. The PDF export capability was utilized to share with personnel within the organization who wanted the report sent to them as an email attachment.