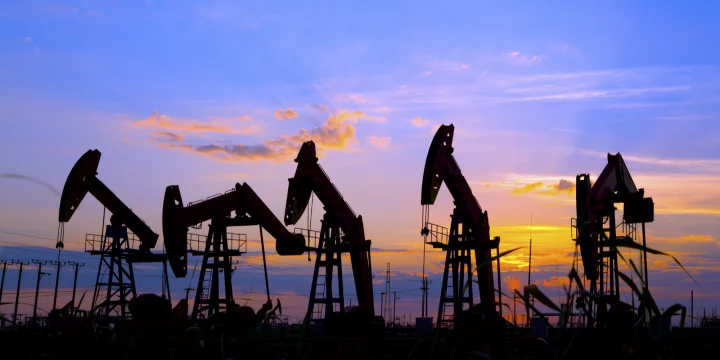
Emergency Shutdown (ESD) Water Hammer Characterization
Challenge
Upstream oil collection networks have emergency shutdown systems to protect against damage; however, when the trip activates, rapid valve closure can cause water hammer to occur. This can cause mechanical damage to the system, vessels and/or cause relief valves or rupture disks to blow, with safety, reliability, and environmental impacts. The challenge faced by oil and gas operators is being able to proactively detect where water hammer happens to focus re-engineering of emergency shutdown (ESD) and equipment. This improves ESD valve and system design, to “build in” long-term improvements and eliminate the problem.
Solution
Detection of water hammer occurrence requires the discovery of well pressure waves with a certain periodicity, amplitude decay, and proximity to an ESD event. Through the use of Seeq’s Asset Capabilities, minimal effort is required to replicate the analysis automatically across all wells to detect such events.
Benefits
Prior to using Seeq, the engineers’ ESD analysis was purely reactive, due to a large number of assets and data per asset. The magnitude of data required for proactive analysis could not be assembled into a manageable workflow with traditional tools.
Analysis enables a focused redesign effort which in turn reduces the frequency of damaged equipment due to water hammer events. This reduces maintenance costs and production losses of 40,000 STB ($2M) per day of downtime. Moving from reactive to proactive management reduces damage and releases to the environment and saves two days of engineering time per incident.
Data Sources
- Process Data Historian: OSIsoft PI
- Asset Structure: OSIsoft Asset Framework
Calculations and Capsules
- The slope of the pressure signal is calculated, from which local maximums are detected and marked with samples. The period between these maximums during hammering are particularly consistent, and thus straightforward to target with Value Search.
- The amplitude of pressure oscillation is also straightforward to calculate with Signal from Condition.
- Pressure oscillation can also possibly be detected via FFT, but the approach to detect periodicity in local maximums is more accessible to a broader user group.
Summarizing Results
ESD occurrences are consistently identified on historic data to proactively identify assets most affected by large pressure hammering and inspection/maintenance prioritization. Moving forward, the operations team is affiliating inspection and failure data with hammering events and characteristics to identify relationships and further optimize inspection and maintenance schedules.