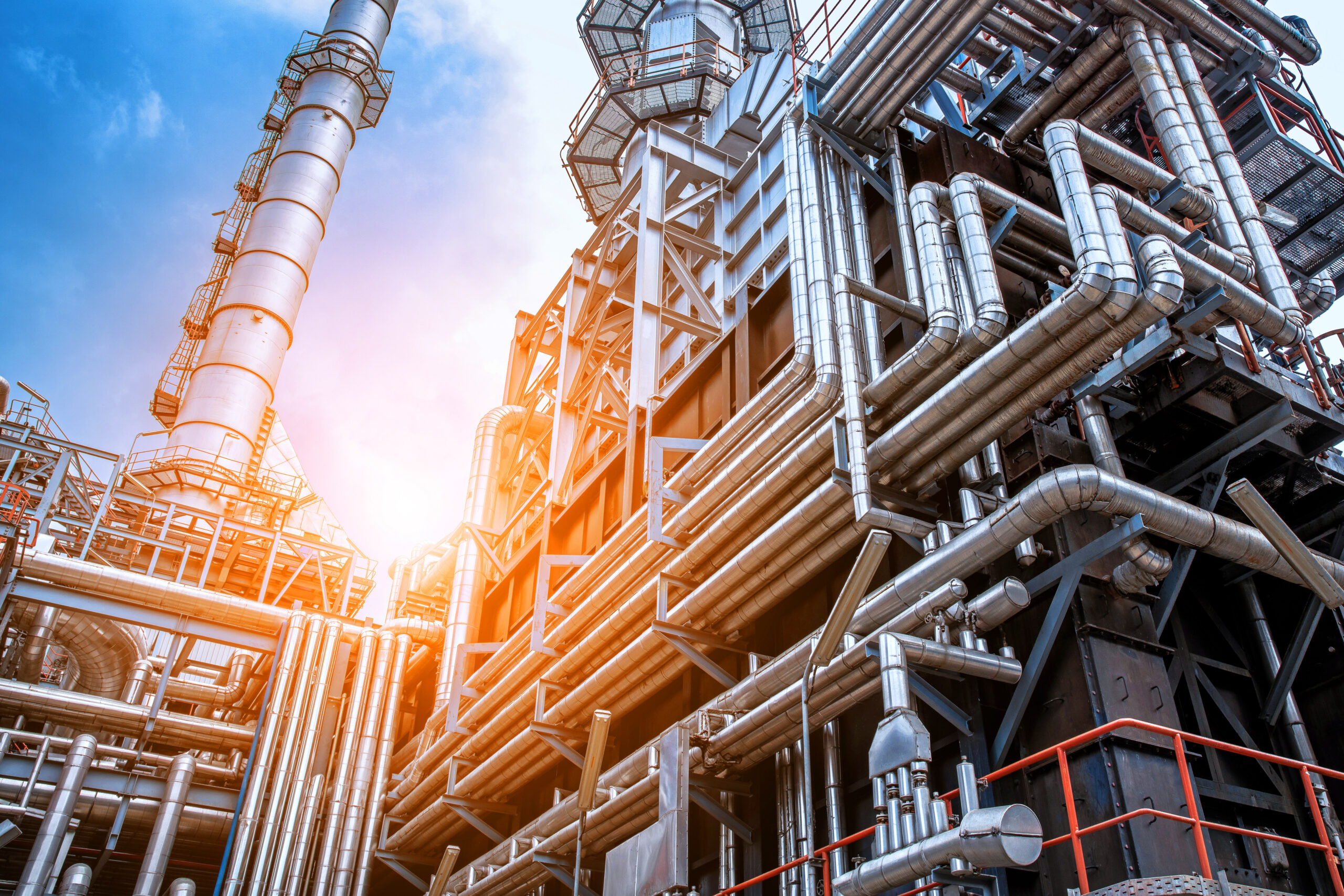
Chemical Reactor Product Transition Optimization
Challenge
Chemical reactors are among the most flexible assets in a manufacturing plant, enabling the same equipment to produce vastly different products by changing reactor conditions. However, the transition period between the production of different products can be costly for manufacturers.
Transitioning a reactor from one product to another causes material to be produced outside of the specification windows for either product. This off-specification (off-spec) or wide-specification material is sold at a severely degraded margin. Therefore, manufacturers aim to minimize both the time taken to transition and the material produced during transition periods to maximize profitability.
This optimization analysis is time-consuming, requiring engineers to sift through years of data to identify specific transitions, overlay numerous reactor and laboratory parameters during those transitions, calculate exact start and end times of the transition, and calculate KPIs to rank the effectiveness of the reactor transition. Thus, the analysis is not feasible at scale using traditional tools such as spreadsheets and historian trending tools.
Solution
Seeq Cortex eliminates many of these time-consuming challenges by enabling SMEs to access all process and quality data required for the analysis in one place. Using Seeq Workbench, subject matter experts (SMEs) can clean process signals, and search for characteristic step changes in process set points and the product grade code to identify each product transition. Conditions containing properties for the type of transition can be filtered, so like transitions can be viewed side by side, whether they occurred weeks or years apart.
By overlaying the quality data against the transition, SMEs can calculate actual start and end time from when the quality parameter went out of specification for Product A and into specification for Product B. Finally, SMEs can filter their transition condition to focus on a single product transition and build a reference profile of the fastest transition time that corresponded to the least off-spec or scrap material produced.
Results
Engineers can use the reference profile as a target for the next transition to significantly reduce transition time.
In one scenario, a specialty polyethylene production unit reduced transition off-spec by 5 railcars compared to historical transitions. By swapping out the transition type to perform the same analysis for each of their other upcoming transitions, engineers demonstrated repeatable savings of 3-5 railcars of off-spec per transition. For a single production line that performed an average of 2 transitions per month, this saved an estimated $850k per year in margin loss due to downgrades.
Data Sources
- Process data: AspenTech IP21, Honeywell PHD, OSIsoft PI
- Quality data: Laboratory Information Management System (LIMS)
Data Cleansing
- Removed outliers and downtime data from analysis data set.
Calculations & Conditions
- Derivative calculations were performed on various signals in Seeq Formula.
- Value Search was used on the derivative signals, using characteristic step changes in controller set points or grade code tags, to identify product transitions.
- Seeq Formula was used to map the starting and ending product grade to each transition Capsule.
- Seeq Formula was used to filter the transition condition for the transition of interest.
- Reference profile was used to build a golden profile of critical process parameters during the transition period.
Reporting & Collaboration
- Seeq Journal was used to capture views for different product types so engineers coming up on a transition could easily click back to that transitions analysis, update the time range, and monitor the current transition.
- An Organizer Topic was built to summarize the results of the transition analysis, showing trends of transitions versus the golden profile, and indicating a step change in the off-spec produced per transition before and after this analysis was performed.