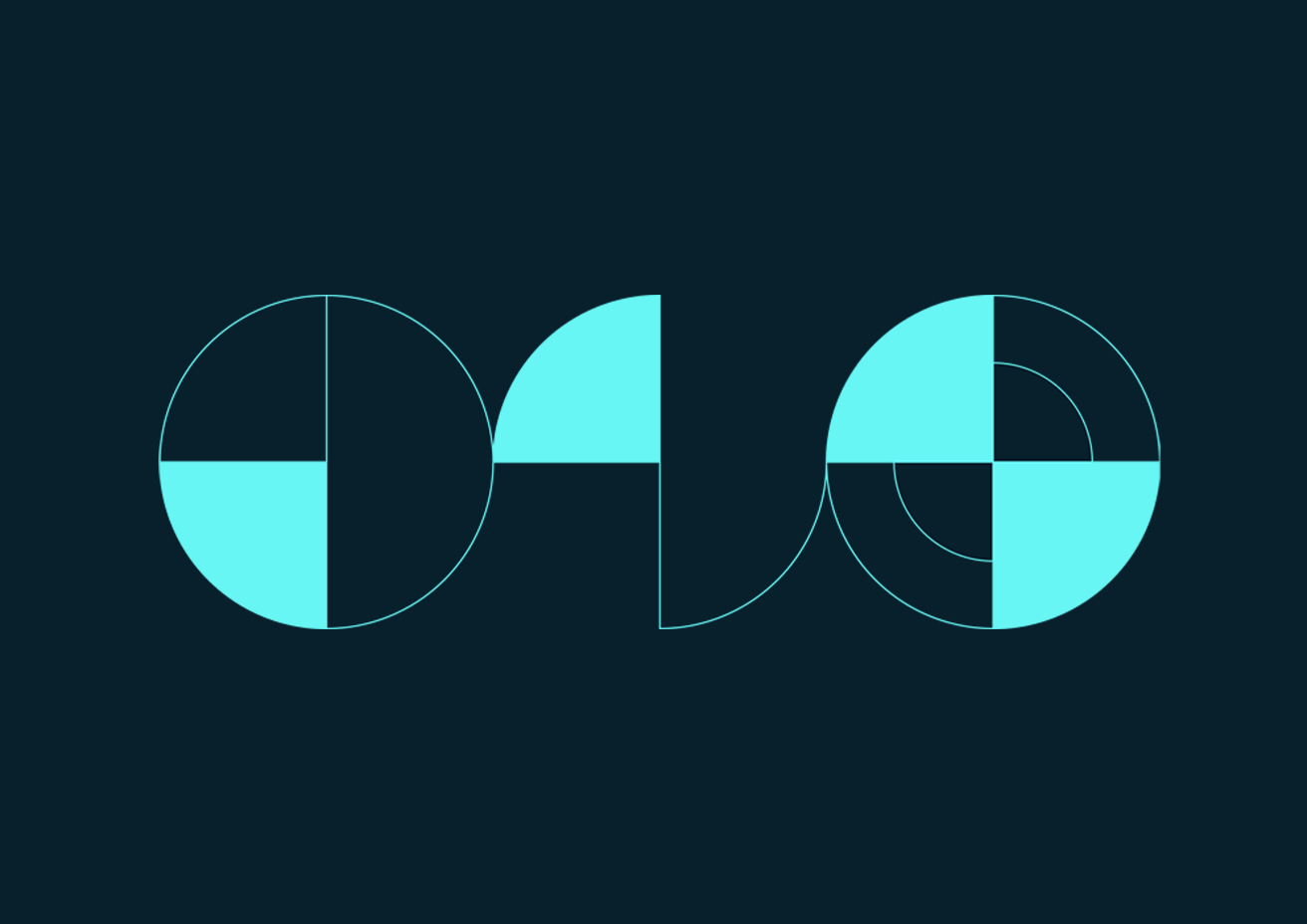
Increasing Operational Efficiency in Upstream Oil and Gas
Beyond SCADA: Optimizing E&P Assets with Time-Series Analytics
Exploration and production (E&P) companies must always strive for best-in-class production asset operational efficiency to manage costs and maximize profits. However, the present environment, in particular, can be a challenge to navigate.
With the global energy transition in full swing, operators are faced with constantly changing regulatory and compliance requirements that demand close attention and agile adaptation. The energy transition is also creating uncertain long-term production demand and rapid fluctuations in short-term demand due to variable global economic conditions, complex geopolitics, and natural disasters.
The oil and gas industry, by nature, will continue to navigate complex challenges and opportunities, making now an ideal time to integrate digital technologies that streamline processes and optimize operations. This is because successful digital transformation increases operational efficiency, reduces maintenance costs, and enhances safety and environmental performance.
Advanced Analytics Platforms Create Insights
At Seeq, we have spent the last decade building our platform to provide industrial analytics and AI for upstream oil and gas operators, enabling enterprise monitoring across limitless assets. The highest value and most easily scalable use cases typically fit into one of three categories:
- Emissions performance improvement
- Production optimization
- Equipment downtime reduction
According to the World Economic Forum, digital technologies will aid in reducing emissions up to 20% by 2030 with minimal capital expense. However, left to outdated software tools, performing the analysis to properly track and mitigate emissions is time-consuming and cumbersome, leading to slow, inconsistent progress.
Conversely, Seeq’s self-service advanced analytics capabilities make it easy to automate and streamline regulatory reporting for easy upload into corporate reporting systems, such as SAP. Once companies are equipped with insights into their emissions on a daily or hourly basis, they can use this information to streamline processes. For example, reducing flaring emissions from various sources, such as blowdown valves, is one of the most common Seeq applications.
Maximizing oil recovery while minimizing costs through improved efficiency and reduced equipment downtime is imperative for operators to maintain profitability in the top—and even more so in the bottom—of cycle periods. By using Seeq’s innovative Capsule Identification technology, users can create smart logic and alerts, incorporating both first principals assumptions and AI to intelligently monitor thousands of assets at a time. These types of alerts empower companies to increase production recoveries, extend mean time between failure for assets, and justify extending test intervals that require asset downtime. The following use cases changed the way teams perform monitoring and maintenance activities in each scenario to minimize cost and increase asset reliability.
Use Case - Hot Oil Sales
Seeq is partnering with companies like Velocity Insight (VI) to minimize end user time to value. In one case, VI helped an operator identify “hot oil sale” instances in a live tank, which have negative financial and emissions repercussions. Hot oil sales occur when oil is drawn from a tank before the produced fluids cool, separate, and stabilize. These events increase emissions, cause rejected loads due to high RVP or BS&W, and present safety risks. It is best practice to allow oil to cool and finish separating before sale.
Identifying hot oil sales is difficult using raw SCADA data alone. Doing so reliably requires advanced data ingestion, smoothing, and analysis tools, like those provided in Seeq.
Leveraging tank fluid level information, Seeq was applied on a DJ Basin dataset to identify hot sales in the absence of direct temperature measurements. Tank drain events occuring shortly after tank fill events were flagged as probable “hot sales,” and two of these are shown in Fig. 1.
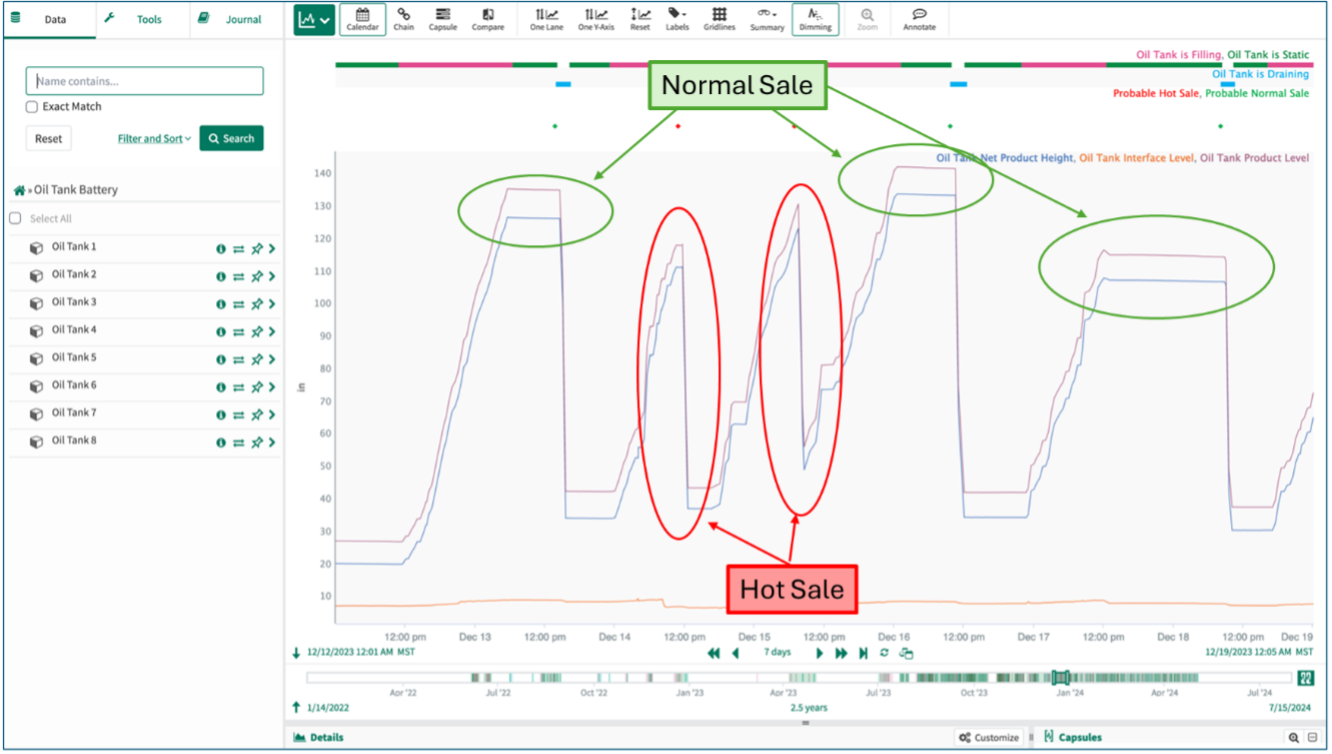
In an eight-tank pad dataset, this Seeq analysis identified 1,100 tank sales from SCADA data and flagged more than 20% of these as probable “hot sales.” These events are easy to see through visual inspection, but the volume of data across large numbers of pads makes automated analysis essential for detection and mitigation.
A separate dataset shows that 6.5% of the loads being hauled from this battery have BS&W > 1%, which is considered out-of-spec under typical DJ Basin oil hauling terms. Rejected loads are typically subject to increased costs for recycling, and penalties levied by the oil purchasers exceed $3-5/bbl. During the 22 month period when this analysis was conducted, this was the equivalent of $70,000 cost savings for the E&P company on just a single pad. Extrapolated across the entire basin, annual costs would be orders of magnitude higher.
Other Applications
Fig. 2 clearly illustrates oil shrinkage, stabilization, and cooling during the static portion of tank fill and tank drain cycles—e.g., between 6:00 3/23/2024 and 10:00 3/25/2024. The shrinkage can be observed as the slow reduction in fluid levels that followed tank fill events resulting from evaporation of light ends. Under normal operating conditions, these volatile emissions are recovered and mitigated by vapor recovery systems, eventually sold through a gas pipeline.
Where insufficient stabilization and cooling occurs before sale, these volatile light ends are emitted during transport from pad to collection point. By combining this data with standard temperature adjustments, emitted volumes can be estimated and mitigated.
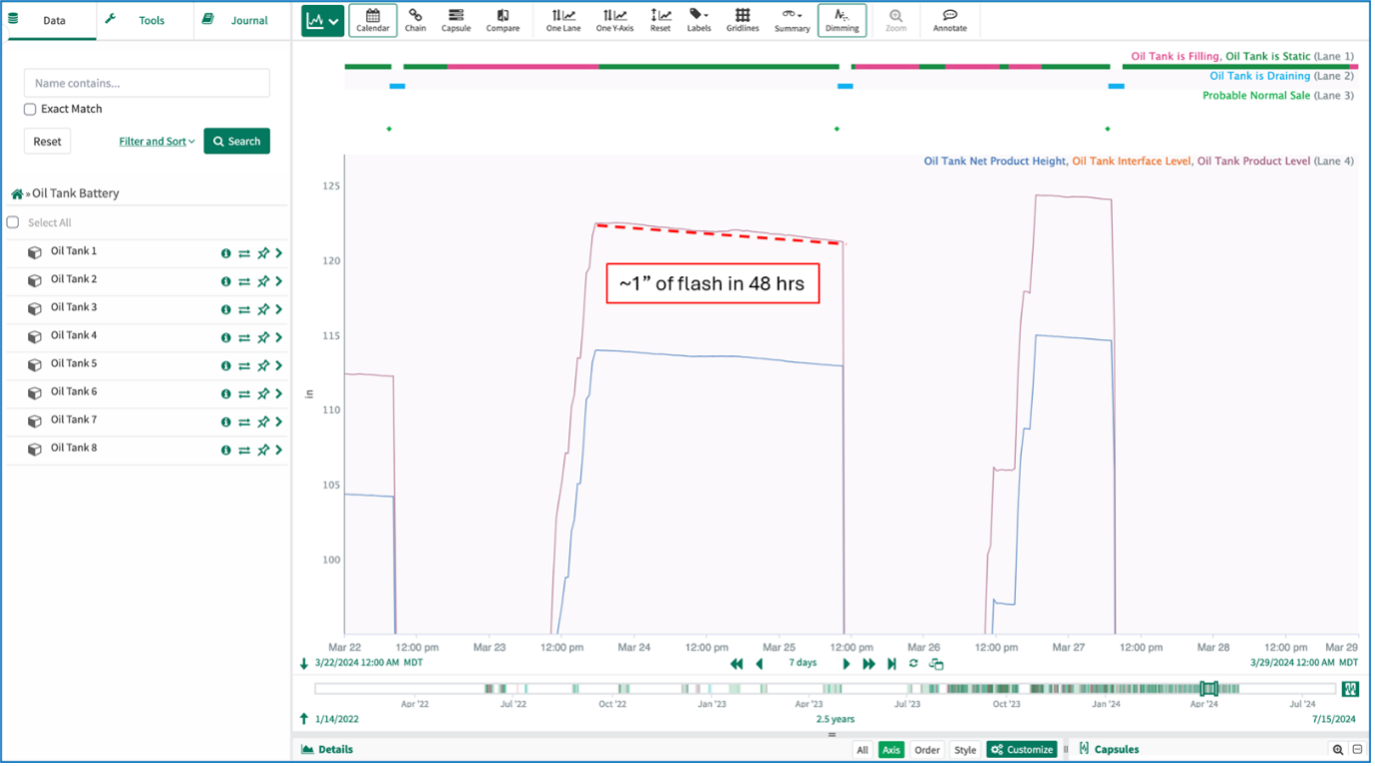
Though there is currently no financial penalty for emissions during transportation, emissions can be estimated by multiplying the shrinkage rate by transportation duration. While best practices—like avoiding hot oil sales—are already employed by industry leaders as they focus on reducing emissions, pending regulations like OOOOb/c are raising the compliance stakes. Seeq’s platform makes monitoring, verification, and reporting possible in a way that conventional tools cannot.
Other potential use cases for E&P companies include identifying separator issues (like stuck dump valves), incomplete plunger trips, gas-locking ESPs, sucker-rod pump failures, and venting/flaring events. Many of these kinds of events have been historically difficult to monitor because they are not directly measured or require multi-step conditional logic to identify, but Seeq’s ability to perform complex analyses on SCADA data makes inferring these probable events possible, similar to the hot oil sales example.
Achieve Digital Transformation and Sustainability Targets
Combining the analytics and monitoring capabilities of Seeq with the upstream O&G knowledge provided by partners like Velocity Insight enables E&P companies to accomplish successful digital transformation with desired results, all the while reducing the time required to achieve net-zero capabilities.
If you are ready to discuss how Seeq can improve your operations to increase production efficiency and reduce emissions, reach out to our industry experts, and schedule a demo today.
View additional upstream oil & gas success stories here.
About Velocity Insight
Velocity Insight is a data analytics consulting firm that focuses on O&G use cases, with deep expertise in E&P workflows across disciplines. The world of O&G data is constantly changing, with a complex blend of legacy tech and modern tools used side-by-side. VI’s team of multi-disciplinary engineers, accountants, landmen, and solution architects has the experience and business knowledge to accelerate the time to impact for tools like Seeq. Reach out directly, or take a look at example solutions.