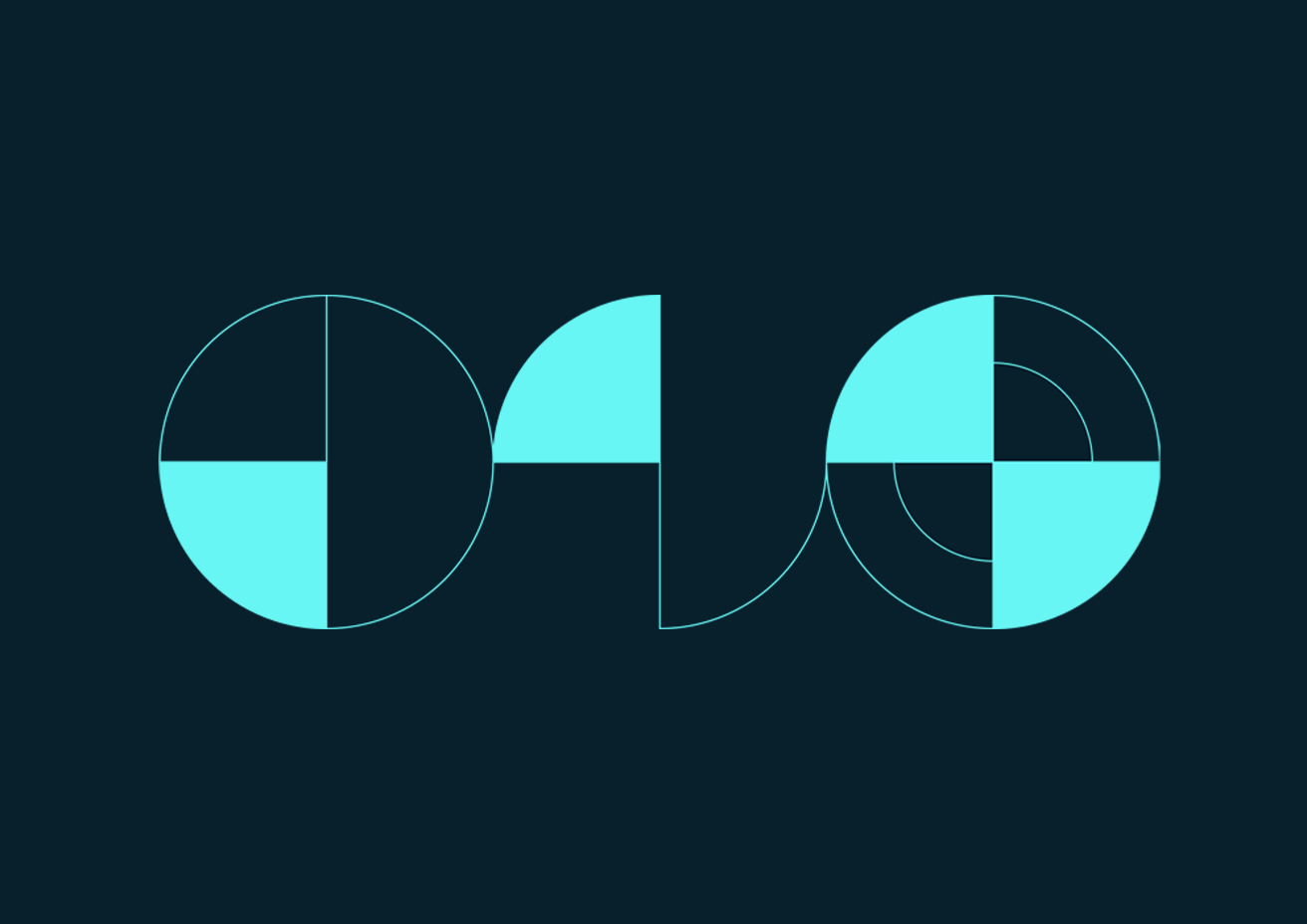
Applying Predictive Analytics for Efficient Equipment Maintenance and Process Quality
Webinar Review: Predictive Analytics 101
To achieve the highest efficiency possible, today’s process manufacturers need to look beyond reactive and descriptive analytics as they only solve a portion of the problem in using data to increase operational performance.
Reactive analytics uses information from events that have occurred in the past to respond to a given situation. This process of looks into a raw set of historical data and applies statistical analysis to gain insights or identify patterns in this past data. With this “reactive” approach to analyzing process data, there is an inescapable lag between the event being analyzed and the action taken to improve future performance. When organizations can only respond to events once a problem has already occurred, they’re unable to prevent any damage from happening.
In a similar way, descriptive analytics also look at the past. The process summarizes information from previous events and creates something that people can easily interpret. Descriptive analytics describe what happened using production dashboards, reports, and KPIs to help people learn from past behaviors. But there’s still lag time and a lack of clear-cut answers on how and when to effectively make decisions that will prevent future performance issues.
Both of these processes provide value, but they don’t solve the whole puzzle. Predictive analytics provide the missing piece by using data to anticipate what will happen, when it will happen, and the actions that can be taken to impact those outcomes. It’s essential to take advantage of a combination of historical, near real-time, and future time series data and analytics to provide process manufacturers with the insight they need to achieve greater efficiency and performance.
There are many uses for predictive analytics to display a projection of future data that prescribes the necessary actions and leads to data-backed decision-making. In a recent webinar, I shared various use cases for predictive analytics at today’s process manufacturing organizations, which I’ve summarized below.
Continuous Chemical Manufacturing Process
Chemical manufacturers can leverage advanced analytics to predict product properties on a finished chemical/polymer property based on upstream conditions. To do this, Seeq seamlessly cleanses the data using filtering algorithms and uses time-series analysis to predict the expected quality parameter.
This empowers operators to see the expected impact of process changes, identify deviations, and quantify impact to calculate the financial benefits. As a result, the subject matter experts at this facility have access to a near real-time projection based on current conditions to inform future process decisions.
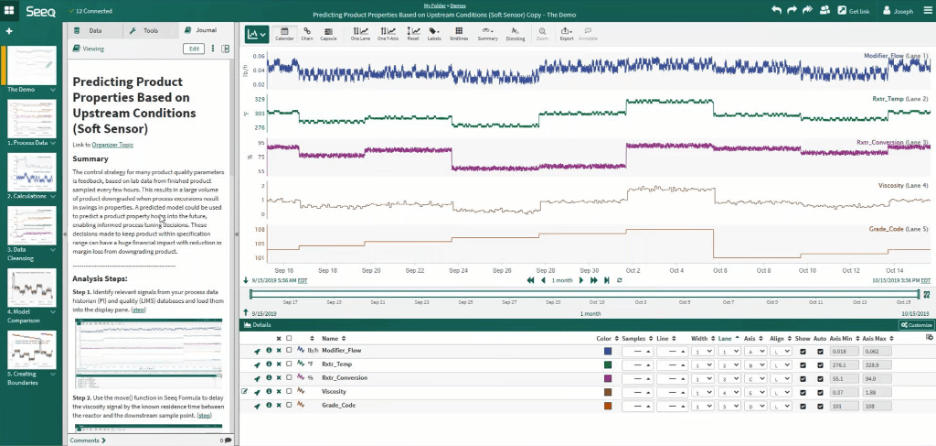
Filtration Membrane Predictive Maintenance
Seeq’s predictive analytics capabilities are driven by advanced algorithm functionality. An organization’s specific workflows and processes are matched within the application to its respective law, theorem, or process design principle to automatically generate KPIs for its data. This enables accurate data extrapolation when expanding to future time frames for insight and analysis.
In another use case, we discussed the degradation of filtration membranes using Darcy’s Law to predict when maintenance needs to occur to prevent unplanned downtime. Over time, fouling of membranes due to ineffective cleaning or degradation with usage of the membrane reduces the overall quality and performance of the membrane, requiring the need for maintenance.
Seeq empowers engineers to quickly calculate membrane resistance using Darcy’s Law to determine fouling over time to build a predictive maintenance and warning schedule. Doing this maximizes the lifespan of the filters while providing minimal impact on operations. This also leads to major improvements in cycle time, yield, and batch quality. You can see exactly how this analysis is configured using Seeq in the webinar recording.
Compressor Health Monitoring and Maintenance
Process manufacturing operations can also be faced with the inability to detect and predict compressor performance issues, which could lead to a catastrophic shutdown of operations or issues with environmental safety. Seeq can be used to monitor compressor health variables to see mechanical degradation or poor performance without manual or tedious time spent looking at data in spreadsheets.
Using Seeq, users can quickly identify leading and lagging indicators of compressor health and monitor compressor health variables continuously to detect poor performance and mechanical degradation. This enables proactive engineering assessments, helping to identify risks and prioritize maintenance activities to reduce the likelihood of a catastrophic failure. Using Seeq in this instance drives long-term cost savings by detecting and preventing similar events in the future.
In this compressor health use case, Seeq enabled data scientists to leverage machine learning algorithms such as clustering to determine the root cause of the equipment failure. The data scientists were then able to deploy the algorithm online to provide advanced warnings of imminent failure in the future, with insights provided in a visual interface directly to the operators and process engineers.
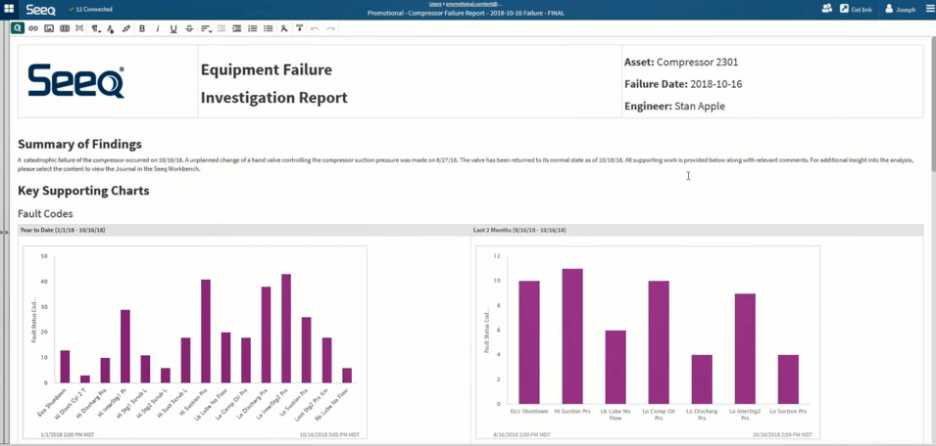
Implementing Advanced Analytics
Manufacturers can obtain the technology required to achieve the insights and actions mentioned in the use cases above by using advanced analytics.
Advanced analytics, and its capabilities for predictive analytics, provides insight into how things are running in near real-time, which can help reduce downtime, poor production quality, and other performance issues. Before advanced analytics, manufacturers would spend time sorting through spreadsheets full of data, which takes valuable time away from implementing any changes. Now, they are empowered to gather, cleanse, analyze, and use this data to make informed decisions faster than ever.
Watch the Webinar Today
With Seeq Workbench, you can share and analyze manufacturing data using advanced analytics to find insights to help improve your manufacturing process. In combination with Seeq Organizer, you and your team can publish the results into dashboards and reports to provide continuous improvement in your organization.
Download the webinar today to see the technology in action. And if you’re ready to see how Seeq can be applied to your operation, schedule a demo today.