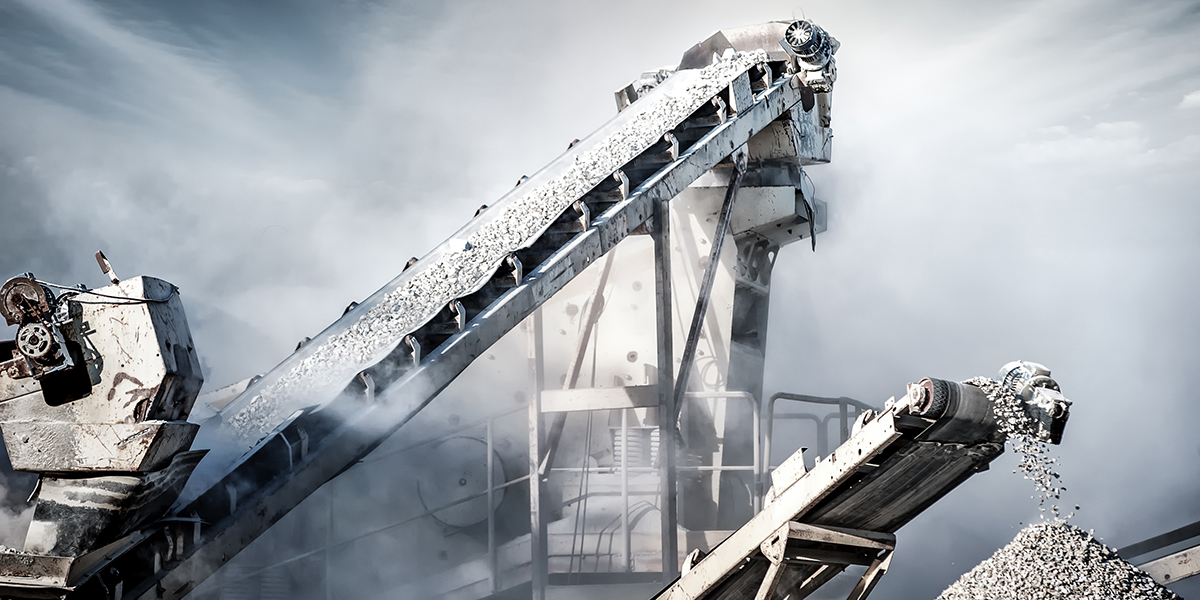
Free Lime Modeling
Customer
S&P 500 company that supplies aggregates and heavy building materials.
Challenge
Cement plants apply lime to the kiln to manage the reaction converting the raw material into clinker, or cement powder. Free lime is a critical process parameter for cement producers. Most cement manufacturers target the free lime to be between 1%-2%. Too high of a reading indicates raw materials and energy are being wasted. But low free lime readings tend to indicate quality problems that can result in significant lost revenue and even potential loss to the company reputation. Being able to make an incremental improvement in free lime can save a lot of money and time in production while safeguarding quality.
Traditionally, cement producers take a clinker sample in a cement batch and send it to a lab to run quality tests. It typically takes at least an hour for the lab results to appear in the historian. Given the delays in lab results, it is difficult for operators to optimize the addition of lime to minimize Nitrogen Oxide (NOx) emissions and keep free lime readings at specified levels.
Complicating things further, the cement industry is under environmental regulatory pressure to use more and more alternative fuels to heat the kiln – such as shredded tires and municipal waste. Due to their varied nature, these alternative fuel sources make it much harder to control the free lime levels.
To save production time and money, a major supplier of building materials needed a faster way to assess the quality of free lime in its cement process.
Solution
Using Seeq, the cement company was able to create an online model for the clinker free lime-based upon the level of NOx, enabling the operator to adjust the fuel addition in near real-time.
The operator creates a “soft sensor,” or model, of the percentage of free lime-based upon the NOx signal. This way, the operator receives a reading of the near-real-time value of free lime and can adjust the process on their control system to reduce fuel waste while still maintaining good quality. Seeq enables the cement company to balance the amount of energy the process consumes (as indicated by the NOx value) without falling below the limit for good-quality clinker.
Data Sources
- Process Data Historian: Wonderware, OSIsoft PI
- Laboratory Data: Process Solutions Canada Limited, Laboratory Data Management System
Data Cleansing
- The NOx and Free Lime signals are filtered using Seeq’s agile filter to smooth the signal
- Model training time range was specified with a Condition
Calculations and Conditions
- Seeq’s Prediction tool creates a model for a “soft sensor” of the Free Lime in the clinker. The input is the NOx signal.
Reporting and Collaboration
- The Workbench Analysis is configured to auto-update as new data streams in to notify the operator on the modeled free lime % in the clinker.
Results
A single cement plant was able to save approximately $600k per year. The energy savings was $300k due to reduced fuel waste to maintain a high free lime content. The quality savings was $300k due to reduced product loss and rework to mix small amounts of the low-quality clinker with the high-quality clinker. Also, preventing poor quality clinker from going to their customers is invaluable for a good business reputation.
In addition, being able to take the model and share it among operators, engineers, and managers enables the company to share insights that can be used in innovative ways.