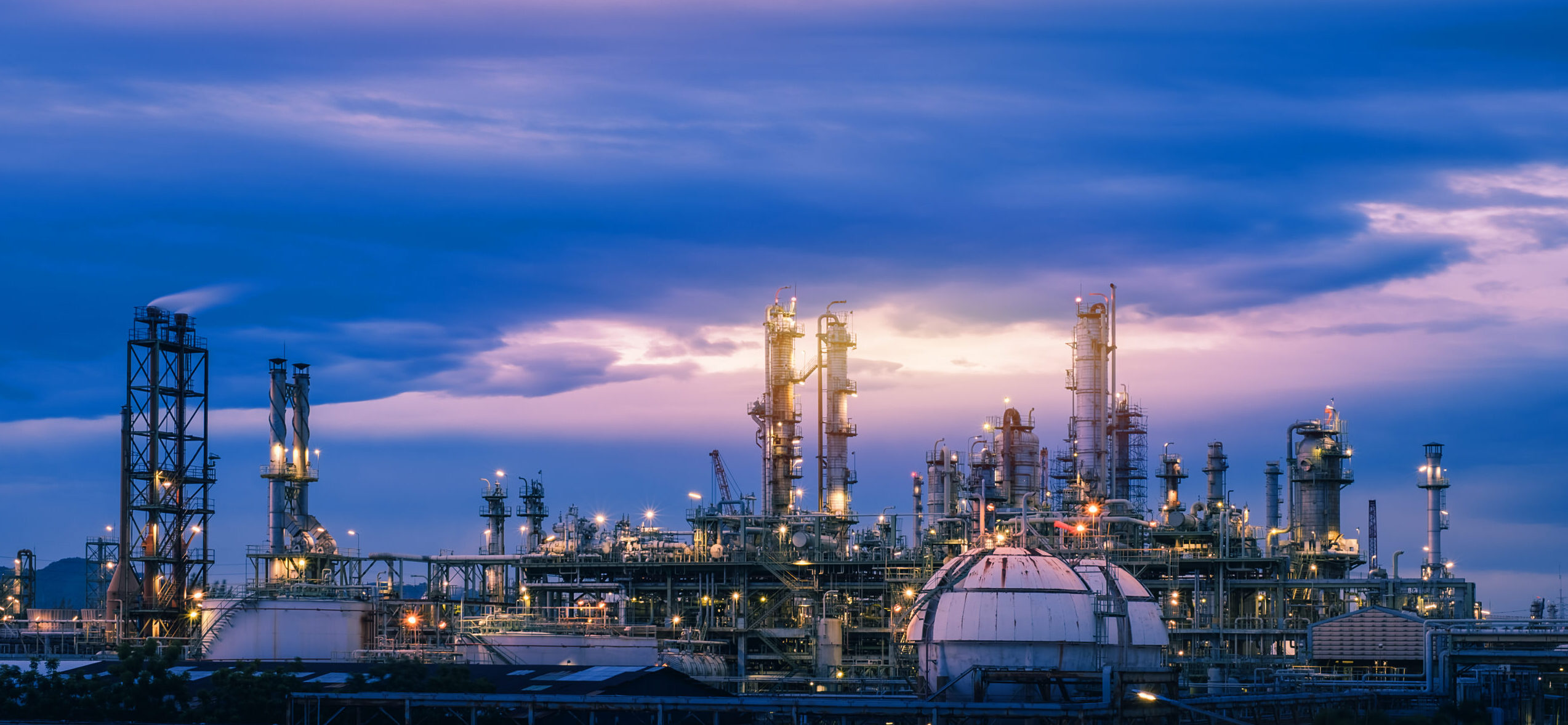
Increase Capacity through Optimal Product Transition Scheduling
Challenge
Chemical reactors are among the most flexible assets in a manufacturing plant, enabling the same equipment to produce vastly different products by changing reactor conditions. However, the transition period between the production of different products can be costly for manufacturers.
Transitioning a reactor from one product to another causes material to be produced outside of the specification windows for either product. This off-specification (off-spec) or wide-specification material is sold at a severely degraded margin. Therefore, manufacturers aim to minimize both the time taken to transition and the material produced during transition periods to maximize profitability.
Engineers can help reduce this transition time and material by optimizing the number and type of product transitions they complete. Building an optimal product cycle order and length takes extensive knowledge of the time, off-spec volume, and downstream impacts of each transition type.
Solutions
Seeq eliminates many of these time-consuming challenges by enabling SMEs to access all process and quality data required for the analysis in one place. Using Seeq Workbench, subject matter experts (SMEs) can clean process signals, and search for characteristic step changes in process set points and the product grade code to identify each product transition.
By overlaying the quality data against the transition, SMEs can calculate actual start and end time from when the quality parameter went out of specification for Product A and into specification for Product B. They can then calculate metrics for each transition, including the total time elapsed and total off-spec product made. Aggregating this data across each transition type yields metrics for the maximum, minimum, and average transition time and average off-spec material produced in a transition.
Results
Performing this analysis gives engineers insight into how much off-spec material was produced and how many reactor hours were used during each type of product transition. Armed with this information, they can iteratively generate a production cycle that takes advantage of the best performing transitions.
One commodity polymer manufacturer reported significant transition time reduction, shortening their average production campaign length by 5%, enabling them to creep unit nameplate production capacity to fill the freed-up reactor hours.
Data Sources
- Process data: AspenTech IP21, Honeywell PHD, AVEVA PI System (formerly OSIsoft)
- Quality data: Laboratory Information Management System (LIMS)
Data Cleansing
- Signals were cleansed to remove outliers and downtime data.
Calculations & Conditions
- Derivative calculations were performed on various signals in Seeq Formula.
- Value Search was used on the derivative signals, using characteristic step changes in controller set points or grade code tags to identify product transitions.
- Seeq Formula was used to map the starting and ending product grade to each transition Capsule.
- Signal from condition was used to calculate the duration of each Capsule and the total off-spec production volume made during each transition Capsule.
- Histograms and tables were used to aggregate metrics across each transition type, calculating the maximum/minimum/average transition duration and average off-spec production during each type of transition.
Reporting & Collaboration
- Seeq Journal was used to document the analysis of historical transition data, as well as the multiple iterations of production cycle calculations that ultimately yielded the best possible production order.
- A Seeq Organizer Topic was built to summarize the results of the transition analysis and presented to the unit business team, making a compelling case for changing the production cycle order going forward.
- The Topic was used to review actual transition losses versus planned at monthly production reconciliation meetings, driving transition performance accountability and sustainability.