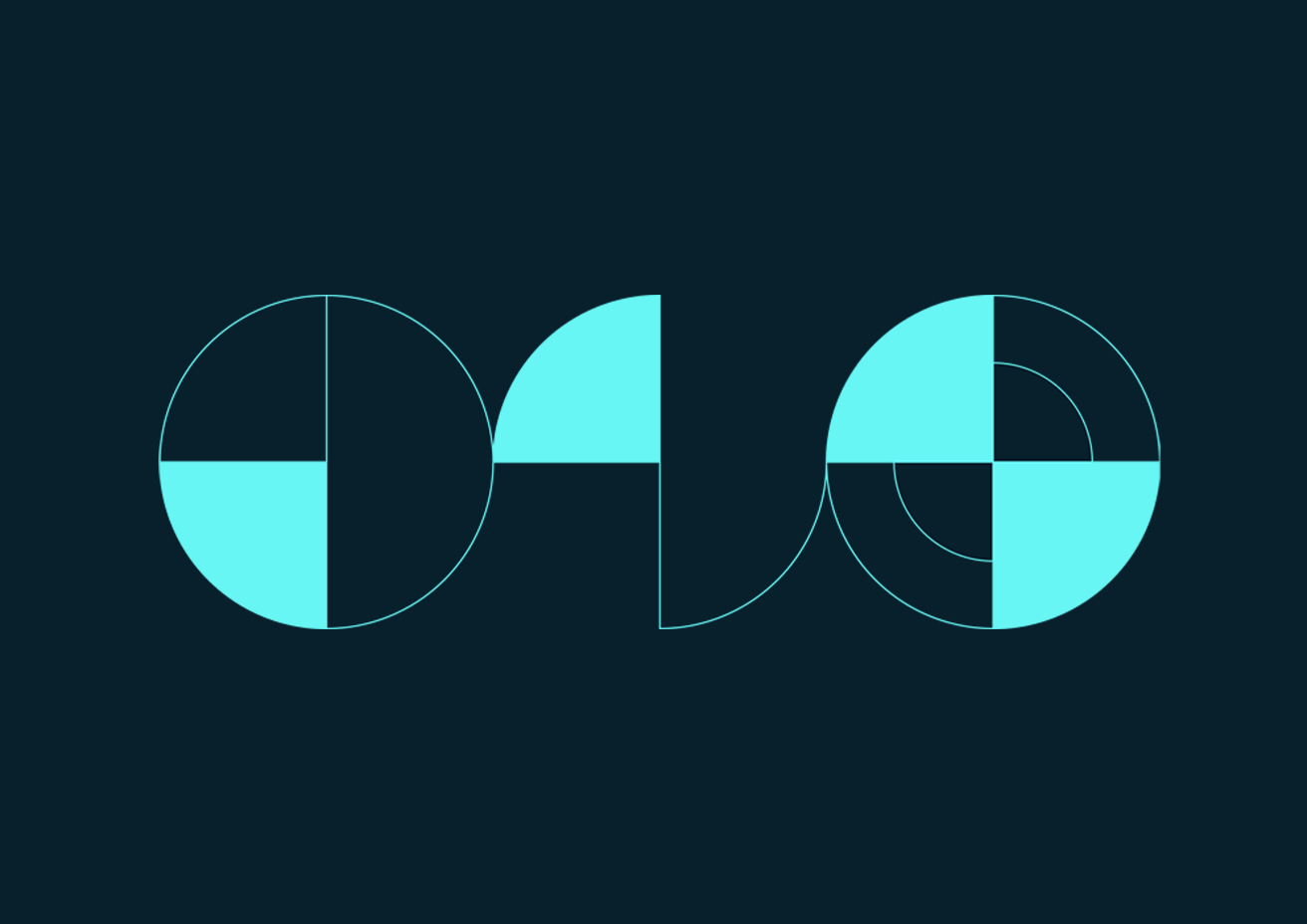
Webinar Recap: Easily Make Data-Driven Decisions with Faster Process Insights
How to Leverage the Power of Seeq Organizer
How much data does your operation collect each day, or even each minute? In today’s world, there is no shortage of methods for collecting process data. Some chemical processing operations have 20,000 to 70,000 signals (or sensors) in simultaneous operation, oil refineries typically use approximately 100,000, and enterprise sensor data signals can easily reach millions.
This can be an incredibly insightful opportunity for your engineers and subject matter experts (SMEs) to take advantage of, but oftentimes, teams are drowning in the pure amount of data flooding in from their sensors and assets without a manageable way to analyze and understand it.
Without a way of cleansing and contextualizing process data, there are missed opportunities for data-backed operational decisions that can lead to major improvements in operational performance and efficiency.
The insight is there—it’s just a matter of finding it, and using it to make a change.
In a recent webinar from Seeq, I joined forces with our VP/CMO Michael Risse to demonstrate how to automate the creation and distribution of near real-time analytics to optimize operational workflows.
Here’s a brief overview of what we discussed in the webinar, available for on-demand download here.
Optimizing Operational Workflows
There are many process workflows that can reveal revolutionary insights with the right data cleansing and contextualization methods in place. In our recent webinar, we share how Seeq Organizer is applied to three substantial workflows to increase efficiency and business outcomes.
1. Daily Standup Meetings
All process manufacturing companies have certain metrics or KPIs that are reviewed on a daily basis to help engineers, management teams, or operations professionals in prioritizing their work for that day.
By implementing advanced analytics, manufacturers can not only immediately enhance their workflows, but also improve decision-making when prioritizing their daily work.
In the webinar, Michael and I outline the key performance optimizations that this capability enables. I also walk through what it looks like to use on a daily basis for various operations.
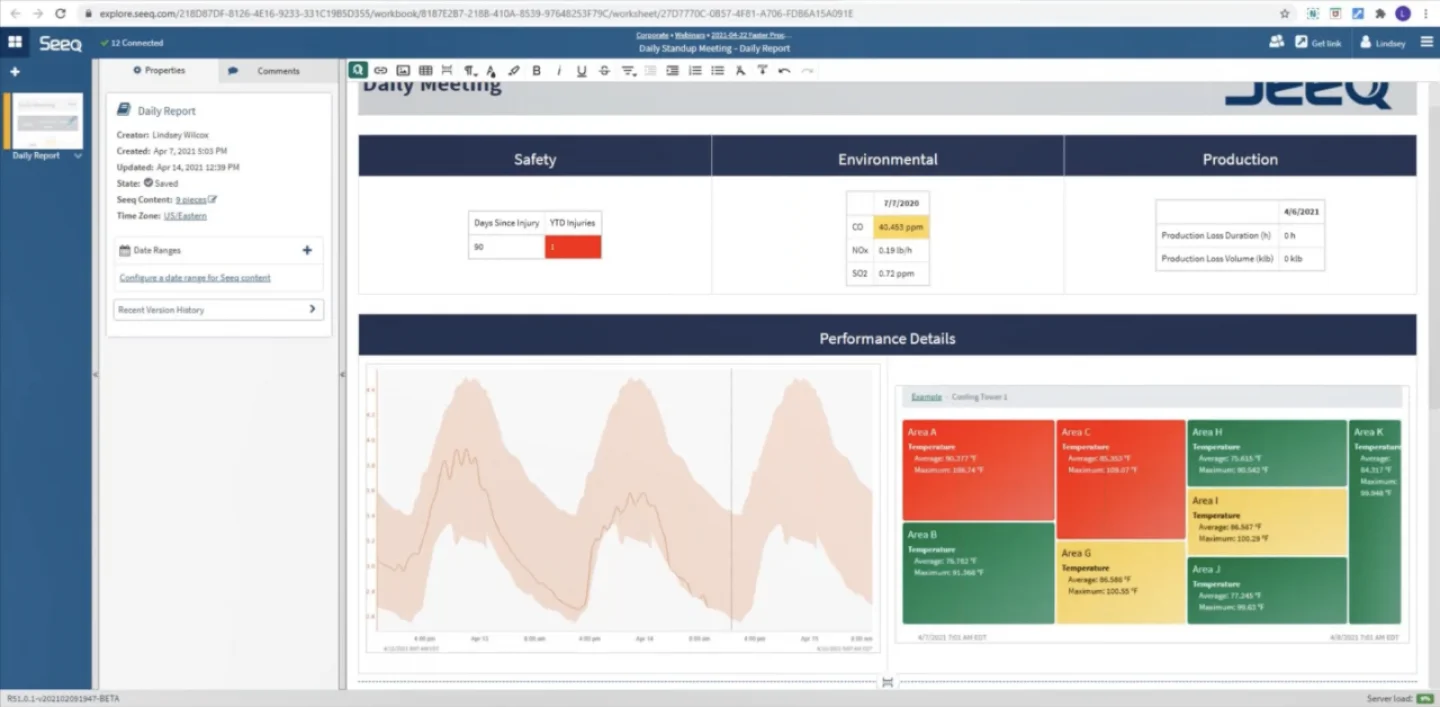
A small-scale refinery uses Seeq’s Organizer for their daily standup meetings. By utilizing the application, they’ve been able to produce an extra few hundred barrels per day out of their operation. This didn’t include any increased labor efforts or additional assets—it was simply from finding operational insight during their “morning coffee.”
2. Asset Performance
Additionally, many process manufacturing plants have hundreds of critical assets, making it impossible to have a single screen displaying a performance dashboard for each asset. And even if that was possible, there’s no way that an operator or engineer would be able to effectively monitor each of those screens and be able to appropriately identify and respond to issues as they occur.
Seeq Organizer enables users to build dashboards and display critical metrics that are updated in near-real time, and provides a way of automatically flagging issues as they occur. Make sure to watch the webinar to learn the key functionalities that come with this capability within advanced analytics.
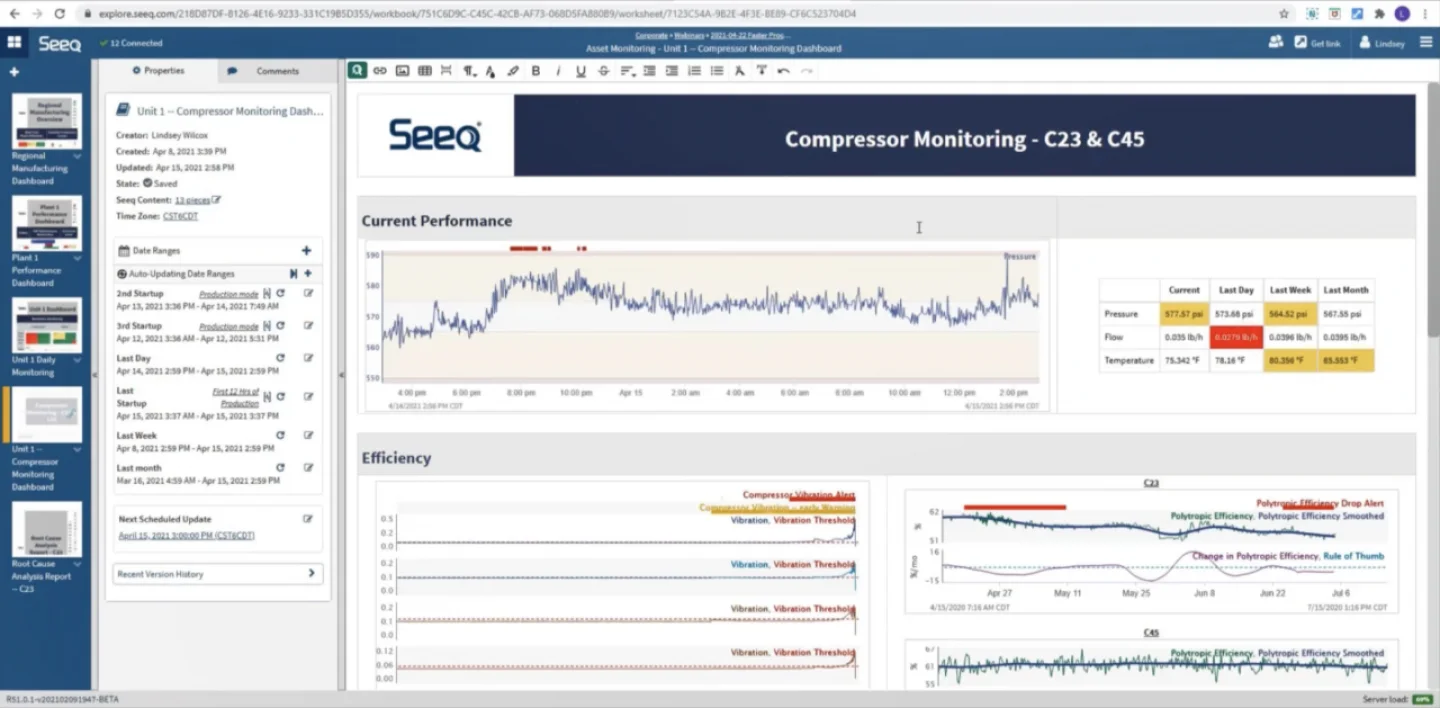
Many pharmaceutical companies use this functionality to monitor batches as they occur, and various industries apply these tools to monitoring emissions or environmental performance in near real-time.
3. Collaboration Enablement
Advanced analytics also contributes to maintaining reliability for data science teams. The key outcome of these workflows includes that multiple teams can collaborate and share information from various sources in a single location, breaking down traditional organizational silos that make this difficult.
By enabling process engineering, maintenance, reliability, and data science teams to seamlessly work together, they can quickly identify the cause of any operational issues and make data-backed decisions on improving production.
In the webinar, we discussed a few examples of this capability in action within various operating process manufacturing plants.
Watch the Webinar Today
With Seeq Organizer, you can share insights across your organization to enable collaboration, monitor key performance metrics, and drive decisions with interactive displays. Data-driven decisions on production, equipment reliability, and sustainability are now easier and faster than ever to create.
Download the webinar today, and see the technology in action.
About the Speaker
Lindsey is Seeq’s Customer Success Manager. She has a passion for process data analytics and empowering customers to improve plant efficiency through the use of cutting-edge technologies. Prior to joining Seeq, Lindsey led the Field Services team at Control Station Inc., leveraging the process operation’s PID controller tuning and monitoring software tools to analyze plant process data in a wide range of industrial environments and industries.